How easy is it to fix broken lighting equipment?
How easy it is to repair a moving light or a piece of LED lighting equipment right down to the level of components on the PCB?
In the current difficult situation the entertainment industry finds itself in, cost savings have never been so important to venues and production companies. Even before Covid-19 effectively shut down most of the business, I’ve noticed a renewed interest in the repair of stage lighting equipment through training enquiries. This has ranged from questions about training in maintenance and servicing of moving lights, to helping a number of people diagnose and verify specific faults with individual components on a particular faulty PCB.
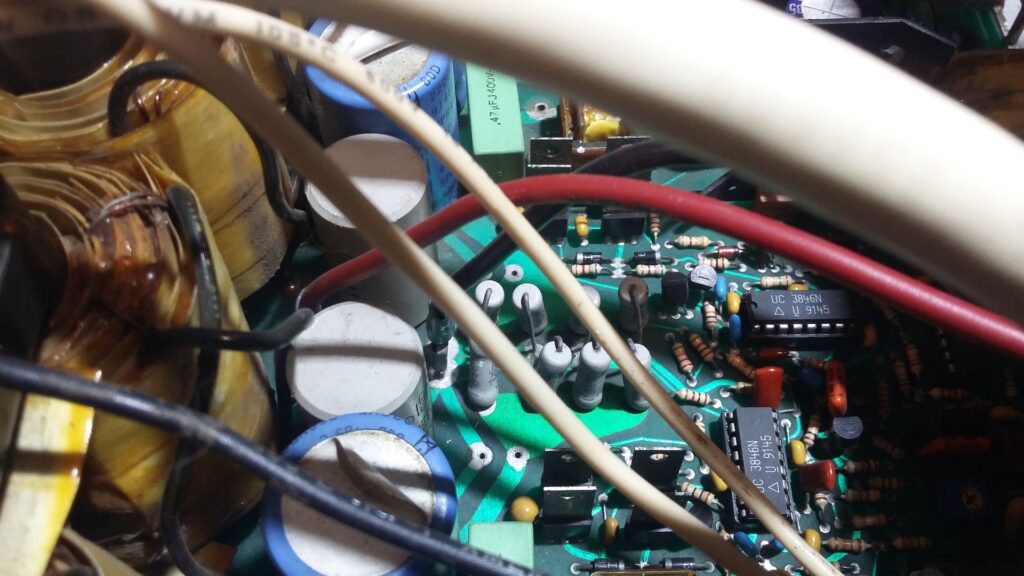
But before we start looking for that one tiny rogue component, what other options are there when you have a fully piece of lighting kit such as a moving light or control console and you are tasked with getting it working again? You’ve moved beyond checking the lamp, fuse, the cable, and the mains supply.
Let’s look at some bigger picture considerations.
Physically broken stuff
It could be a cracked casing, sheared fixing, or just a missing handle, but there are plenty of things that can be repaired at the simplest level like this – if you can get replacement parts. This kind of repair is outside of routine maintenance tasks such as replacing a lamp or an air filter, but often doesn’t require an in-depth knowledge of electronics or even fault diagnosis. It’s broken, it’s obvious and you just need a fit a new part. If the piece of equipment is out of production and parts are not available or expensive, then consider using parts taken from a donor.
The key skills needed here are to be able to identify a busted thing, and fit a not-busted one.
There is also a practice related to this, which is to make a working item from several broken ones. One example from not that long ago: I worked a group of twelve unusable CM Lodestar 1T motors into eleven working motors that were then certified by a 3rd party LOLER testing house and put back into hire stock. Some people like to have a go at this by buying job lots of older broken fixtures and parts from a hire company with a view to getting themselves some moving lights on the cheap.
A word of warning: Hire companies are not in the habit of selling off something that is still viable to them. This means that there is a lot of risk in buying job jots and hoping for the best.
Board or assembly swaps and similar fixes.
This type of repair is very common for in-house technicians in a venue or hire company. The problem might be a faulty sensor, a ballast, a power supply, or a specific ‘board’ that fulfils a particular function. The method of diagnosis is usually to identify the fault based on symptoms and narrow it down to a sub-part of the equipment. This is often then verified to be the problem by way of substitution (e.g swapping in a working part) and the repair made good by replacing the faulty assembly or PCB in its entirety. This working part can either be sourced new from the manufacturer or from a donor. One handy tool to have up your sleeve in this case is a known-good working part, for example a sensor or PCB taken from another fixture. However, be careful not to mis-diagnose the source of the problem and unwittingly blow through a load of working parts by fitting them to a faulty piece of kit.
Key skills required are to understand roughly how the equipment functions, design and carry out a suitable test and verification to identify the faulty part, and fit a replacement. This is a common level for technicians that I work with and teach, particularly if they have some good overall technical understanding but perhaps are not yet confident in tackling specific pieces of equipment. This is often the case for moving lights and other complex kit.
Component level repair
This is a much less common skill, confined to a smaller number of specialists. There are reasons for this. Firstly, the repair may end up being as simple as replacing a faulty component but identifying that component takes a high skill level and, more importantly, time. Time multiplied by a high skill level usually equals a high cost. This is why board or assembly swaps are the norm in the stage lighting business, similar to practices in the world of modern auto-repair. Secondly, compared to this potential cost of labour and those that come with the loss of utility, assemblies and PCBs are actually relatively cheap. Not taking the time to pin down an individual component but instead ripping out a whole PCB and swapping it for a working one is fast and gets the kit back up and running. Time spent waiting for parts deliveries is roughly the same but the diagnosis and fitting time is commonly much decreased.
So, why would you even try to repair at component and PCB level?
If you have time, but limited cash, then a ‘cheap’ repair might be attractive. The idea that that a moving light that cost many thousands when new might be revived by a part that costs a few pence seems like a great deal. And it is. When that happens. If the replacement assembly is very costly or not available at all, this also makes component level repair attractive. There are certain parts that manufacturers sell as a complete unit, making each one quite expensive, when the problem you need to solve is limited to a small part of that assembly.
Get help fixing up your kit.
On Stage Lighting provides specialist repair training, both physical and digital. This can be a day workshop at your venue where we collaborate with you in tackling your maintenance and repair needs but with the focus on learning the techniques for yourself. At the other end of the spectrum, I run 1-1 digital tutoring sessions helping people with a wide range of individual learning needs including fault diagnosis right down to component level. Have a look at the different kinds of learning options we offer.